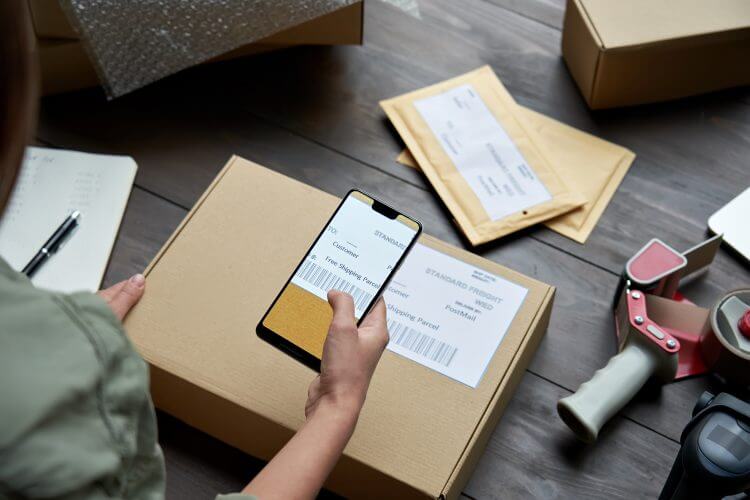
If you run a fabric store, you know how difficult it is to manage your inventory.
With so many different kinds of fabric on your shelves, keeping all of your stock moving and ordering the right amount of replacement stock can be a challenge. And because you have so much inventory to manage, track, and move, you need to establish a solid barcoding system.
Understanding barcoding products for better inventory management can help you take the next big step toward your fabric store’s growth and competitive advantage.
You need a painless, affordable, fast, and error-free system to manage your inventory count, status, and information. Barcoding spares you from manually entering extensive product information every time you move, sell, or buy inventory — and saves input time and employee costs.
But to learn how to implement a barcode system for inventory at your fabric store, you need to understand the processes, techniques, and tools required to do so. In this blog, we’ll explain the importance of barcoding your inventory, and how to set up a highly efficient barcode inventory system for your business.
How Does a Barcode Inventory System Work?
Learning how barcode systems work and how to implement a barcode system for inventory makes you more effective in running a retail business. Barcodes are an integral part of supply chains, inventory management, and warehousing.
When a customer comes into your store, they select a product — whether it’s fabric, thread, or another sewing accessory. Simply scan the barcode labels printed on these items, and all of the necessary product information automatically appears on the interface of your point of sale (POS) system: product details, quantity, and price.
Not only does this system speed up checkout, but it reduces the chance of a billing error. A barcode system keeps your inventory moving and improves the shopping experience for the customer.
A barcode inventory system works by tracking products in stores, warehouses, and during transit by attaching electronically generated barcode labels that contain specific information about products. The barcode contains a unique identification number that distinguishes products from each other. When labeled products are scanned, the information on the barcodes are read by your point of sale system.
Barcoding simplifies inventory updates when a new item is added or an old one is moved out. With the integration of technologies such as RFID, GPS, and sensors, it assists online businesses in tracking the location of the stocks in the warehouse when orders are received and while shipping. Barcoding also helps you accurately track inventory count and movement status when you have inventory stored at multiple locations.
What Is a 1D Barcode and a 2D Barcode?
A one-dimensional barcode (1D barcode) is the type of inventory barcode you might typically think of, with black horizontal lines and spaces between the lines in the shape of a rectangle. Scanning the barcode produces a number, which can be looked up in an inventory management database. These systems are essential for inventory accuracy.
A two-dimensional barcode (2D barcode) typically contains dots and patterns (like a QR code), which allow for storage of more complex information, such as a website or image. These barcodes can typically be scanned with a smartphone.
What You Need To Implement a Barcode System for Inventory at Your Fabric Store
Before you learn how to implement a barcode system for your inventory, you need to be familiar with the materials and tools you need.
Barcode Software
Standalone barcode inventory software (or an integrated inventory management system) with a built-in barcoding module allows you to generate barcodes, print receipts with a connected printer, and store/manage all information about products. Barcode software also integrates with scanners to receive and update information during barcode scanning.
Barcode Labels
Barcode labels are the physical prints of electronically generated barcodes. Labels are printed on a special sheet or roll. Barcodes are codes usually represented by black bars printed on white background.
The most popular types of barcodes include:
- UPC (Universal product code)
- EAN-13 (European article number)
- Code-128
- QR Code (Quick response code)
- Data matrix
The UPC is the most commonly seen barcode type in North America, but the QR code is increasing in popularity due to its easy scannability on mobile devices.
Barcode Printer
A barcode printer is an inkjet or laser printer with features to print barcodes of all sizes.
Barcode Scanner
A barcode scanner is a hardware device that scans, reads, and transmits the information from barcodes to your inventory management system, barcode software, or computer. These devices fall into the category of automatic data capture (ADC) technology, and their usage grows every year.
How To Set Up a Barcode Inventory System for Your Fabric Store
Follow these steps to set up a robust and error-free barcode inventory system for your fabric store.
1. Name and Code the Products
You need to assign codes to each product according to the naming convention practiced in your industry.
These are some attributes of fabric you may use in naming and coding:
- Material
- Color
- Style
- Length and width
- Manufacturing date
- Manufacturing location
This information needs to be put in the inventory management system or the barcode software — if you already have the product information in excel sheets, you can import it.
Based on the comprehensiveness of your product information, decide whether you need a one-dimensional barcode (storage capacity 14-28 alphanumeric characters) or a two-dimensional barcode (up to 7,089 alphanumeric characters). Use standard abbreviations to save characters. For example, small can be coded as “s” and medium as “m”.
2. Generate Barcodes
Once you have put all the information in the barcode system, the software can automatically generate barcodes that can be downloaded for printing. Barcodes are unique to products, so make sure you choose the appropriate type of barcode (UPC, EAN, GS1, etc.) according to the product type and size.
3. Print Barcodes
Next, you need a label printer to print your barcode labels. You can choose to buy your own label printer (one-time investment) or get the prints from third-party barcode label printers (which is time-consuming and often comes with security risks).
We suggest having your own printer for faster access and better security. Depending on your product type, purpose, and security needs, you can print labels of different sizes. After printing the barcode, check for scannability before pasting on the products.
4. Label Products
Before labeling a product with a barcode sticker, find a spot to place it that is visible and free from constant friction that might damage it. The standard recommended place for sticking barcodes is the lower right quadrant on the back of the products. If you follow this practice, it’s easier to find the label and expedite the scanning process. Barcodes can be placed on fabric items using stickers or tags.
5. Scan Barcodes
You need a barcode scanner to read the information stored on barcodes and communicate it to the software. When the sell order is received, and you need to dispatch the item, you can check your barcode inventory software to locate the product.
You can then scan the barcode on the product, and the barcode system automatically updates the status of the product as “sold” and updates inventory information. Using an inventory barcode scanner saves a ton of time and effort in your inventory tracking, as you can minimize the amount of manual entry.
Digitize Your Inventory by Implementing a Fabric Store Barcode System
Modern small businesses are continually improving the ways in which product data is collected, printed, and transmitted. With the steps outlined above, you’ve learned how to implement a barcode system for inventory.
Barcode inventory system technology is faster, cheaper, and more efficient than manually entering product information — and it’s revolutionized supply chains and inventory management processes in small businesses.
Barcoding technology is getting even more sophisticated with time. With automated barcoding scanners with laser beam sensors, you may not even need a person to scan the products manually. Inventory on conveyor systems is automatically scanned and unloaded with installed barcode scanners. With a well-implemented software, you can provide better customer service and faster deliveries, and unleash error-free inventory management.
Barcode scanning technology works in tandem with modern point of sale systems. LikeSew is an all-in-one cloud-based point of sale system that uses barcode scanning technology to make customer transactions quick and easy. Designed specifically for sewing and fabric stores, LikeSew has all the features you need to run your business. Request a demo today!