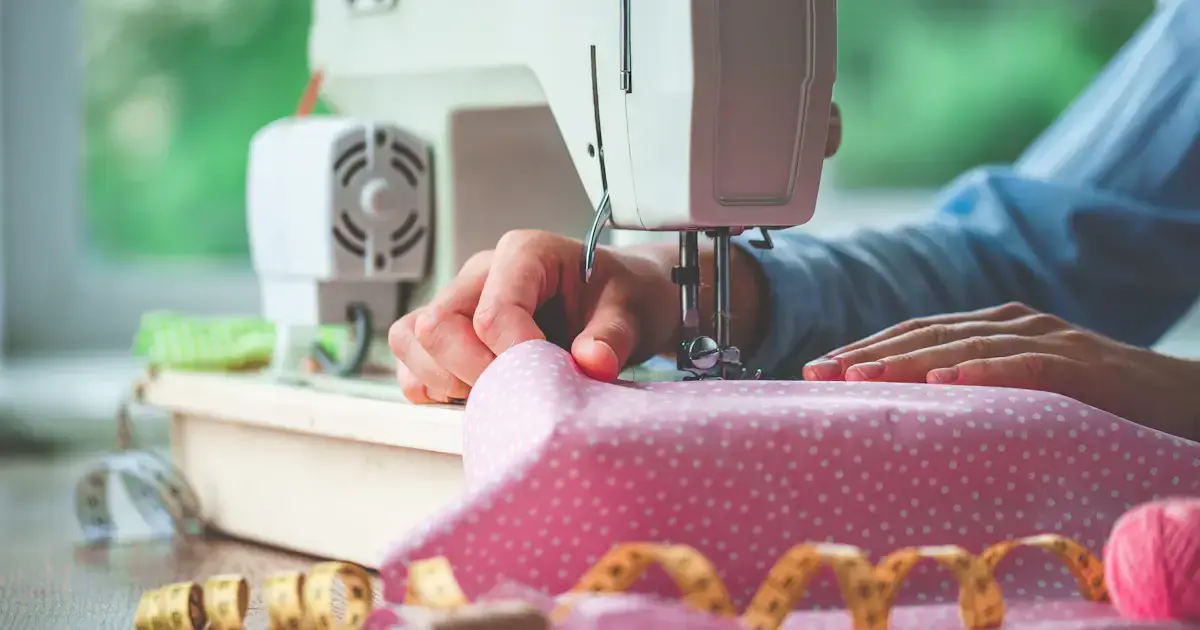
If you’re looking to boost your bottom line, sewing machine repair services are a great addition to your fabric store.
If you sell sewing machines, offering repairs gives customers peace of mind — they know if they have an issue, they can bring their machine back to your business to have it repaired. But even if you don’t sell sewing machines, repairing them brings in added revenue and performing quality repair work increases customer loyalty.
To successfully manage sewing machine repair, you need the right equipment and the right strategies. In this blog, we’ll list essential sewing machine repair tools and go step by step through the management processes you need to add repair services to your business model.
Let’s get started!
Essential Tools for Sewing Machine Repairs
The following tools will help you solve many of the problems you might encounter with sewing machines.
1. Screwdriver Set
Screwdrivers are used to disassemble a sewing machine and reassemble it again. You’re most prepared if you have both Phillips and flathead screwdrivers, and if you have a few different sizes, as the type and size of screws can vary. Some screwdrivers have magnetic tips, which make you less likely to lose small screws.
2. Multimeter
A multimeter is a small device used to test electrical properties, including voltage, current, and resistance. They’re useful in diagnosing electrical issues in sewing machines, and in ensuring a machine is safe to use and in working order.
3. Lint Brush
A simple but important tool, a lint brush keeps the machine clean and functioning properly. Use a lint brush to remove lint and dust in the machine, preventing clogging and keeping the machine running smoothly. If a machine has a lot of buildup of lint and dust, you might need to use a small vacuum to remove it.
4. Oiling Kit
Sewing machines need oil to remain lubricated and reduce wear and tear. An oiling kit usually consists of oil, applicators, and cloths to help apply the oil to the machine. Regularly applying oil to a machine helps prevent rust and friction and keep the machine working at full capacity. Common rules of thumb are to oil a sewing machine after about 3–4 bobbin changes, after 8 hours of sewing time, or when your machine is louder than usual.
5. Tweezers and Needle Nose Pliers
Sewing machines are intricate pieces of hardware with lots of moving pieces. Tweezers and pliers are useful in fixing small parts and issues with threading without causing damage to the machine.
Management Tips for Efficient Sewing Machine Repairs
Just as important as your process for repairing sewing machines are the management processes in place to facilitate the repair. You might excel in doing repairs, but if you can’t keep track of which machine belongs to which customer, can’t stay on schedule, or if you don’t keep customers in the loop, you’ll struggle to find consistent repair work.
In this section, we’ll go over the most important strategies to implement as you complete sewing machine repairs at your fabric store.
6. Set Up a Repair Station
Your workflow will be most efficient if you create a workspace specifically for sewing machine repairs. Store the tools you use for repairs in this area for easy access and to prevent misplacing them. Make sure your repair station is well-lit and clear of clutter and hazards, too.
You also need sufficient storage space for sewing machines that need repairs. Set up shelving next to your work station so you can easily access these machines to perform repairs.
Related Read: Vacuum Repair POS: Top 3 Solutions on the Market
7. Train and Develop Skills
It’s important to invest in training — both for yourself and any staff who may be repairing machines — in order to refresh your skills and stay updated with new sewing machine models. You can take online sewing machine repair courses to sharpen your skills and enhance your credibility.
Apart from formal training, offer necessary instructions and help staff work through issues while they’re doing repairs in store to help them learn and speed up the repair process. You can also offer repair tips to customers to help them do small repairs on their own, which will help you build trust.
8. Utilize a Point of Sale System
The best way to manage sewing machine repairs at your fabric store is with a point of sale (POS) system. These machines automate processes that retail store owners used to do by hand — saving you time and money. Some POS systems have general features that can be used by businesses in a variety of industries, and some have industry-specific capabilities.
A POS system designed with fabric stores in mind offers customized features to make running your store easier — including features to help you manage sewing machine repairs.
Some of these features include:
- Work orders/service scheduling
- Inventory management, including replacement parts
- Customer record keeping
- Payment processing
While using a POS system may be an adjustment compared to the way you’ve run your fabric store in the past, you’ll soon find it’s much easier than keeping track of things manually.
Related Read: Quilting Inventory Management: 5 Best POS Providers
9. Implement a Scheduling System
A fabric-store specific POS system offers a robust scheduling module to track work orders. This helps you keep track of the order machines were brought in and the order they should be worked on to ensure no one has to wait too long. This way, you can prioritize urgent repairs according to your customers’ needs.
10. Market Your Sewing Machine Repairs
To successfully launch repair services at your fabric store, you need to engage in marketing efforts. Social media is a great place to get the word out about these services, but first consider which platforms your audience uses and what content will capture their interest.
Many quilters use Facebook. You can create posts to let customers know you offer sewing machine repairs, and even create video demonstrations. Show customers how to perform simple repairs on their own and let them know that if they need more significant repairs, they can bring their machine to your store.
You can also use signage and posters within your store to let customers know you do repairs. If you sell sewing machines, let each customer who purchases one know they can bring it back into the store for repairs if necessary.
Related Read: Fabric Store Marketing: 8 Beginner Tips
11. Communicate With Customers
Customer communication should be a top priority when it comes to repair work — people want to know how long they’ll be without their machine and to be updated throughout the process if repairs take more or less time than expected. A fabric-store specific POS system helps you automate communications with customers to keep them updated throughout the process.
You may not always know exactly how long a repair will take, and you may discover additional issues you weren’t aware of. It’s impossible to give a customer an exact timeline for how long a repair will take, but do your best to provide the most accurate estimate possible — and make sure to be clear and honest in your communications.
Even with effective processes in place, there will inevitably be issues with repairs. Create multiple channels customers can use to seek answers to their questions, including text, phone, and email. You can also use these channels to follow up with customers after a repair is complete to make sure their machine is still running smoothly.
Related Read: 5 Essential Retail Policies That Will Help Your Business Succeed
Top 5 POS Providers for Fabric Stores
There are many POS providers on the market, each with strengths and weaknesses. Here are our top five POS picks for your fabric store.
Like Sew
Like Sew is tailored for fabric stores and allows you to manage your entire business from one place. It includes features for fractional yards, workshop registration, work orders, access to vendor product catalogs, and more.
Pricing: Contact for custom pricing.
Square
Square is a simple, intuitive platform that’s ideal for small businesses. It’s adaptable to a variety of retail businesses, including fabric stores. It’s easy for staff to learn and operate, meaning you can get started with it quickly.
Pricing: The most basic plan is free, with transaction fees.
Shopify
Shopify is a versatile POS platform with robust features for both in-store and online sales. It includes access to hundreds of external apps you can customize for your business.
Pricing: Cost starts at $29 per month.
Lightspeed
Lightspeed is a powerful cloud-based POS solution with detailed reporting and support for multiple locations.
Pricing: Cost starts at $89 per month, with additional fees.
Clover
Clover is a customizable POS solution with comprehensive inventory management features and a straightforward setup process.
Pricing: Custom pricing is available upon request.
Manage Your Sewing Machine Repairs With Like Sew
Efficient and profitable sewing machine repair requires the right knowledge, tools, and operations.
But before you begin offering repairs at your fabric store, make sure you’re equipped with everything you need to get started and you’re prepared to provide customers with excellent service. If customers have a great experience, they’re likely to tell their friends — but the same is true if they have a bad experience. To create positive publicity, put effort and care into each and every repair.
These strategies will help you manage repairs with greater efficiency and less frustration, but to get started, you need a robust POS system designed specifically for fabric stores: Like Sew.
Like Sew’s all-in-one POS platform has features for work orders, scheduling, inventory management, payment processing, and more.
To see Like Sew in action, schedule a demo today!